When it comes to jobsite health and safety as well as state and federal compliance, it's important that contractors keep hazardous waste developments on their radar. Maintaining an ongoing understanding of these updates also helps contractors stay aware and informed of coming changes, so they can solicit their knowledge and support when the process starts again. The following is an update on OSHA standards related to working around lead-based paint and crystalline silica. The information below was collected and presented to the Remodelers Council of the Master Builders Association (MBA) of King and Snohomish Counties on June 16, 2016 by Al Audette from the Building Industry Association of Washington.
OSHA is issuing new standards for workers exposed to hazardous materials—specifically lead and crystalline silica. "The previous exposure limits were outdated and did not adequately protect workers," said Assistant Secretary of Labor for Occupational Safety and Health Dr. David Michaels in an OSHA news release. "Limiting exposure to silica dust is essential. Every year, many exposed workers not only lose their ability to work, but also to breathe. Today, we are taking action to bring worker protections into the 21st century in ways that are feasible and economical for employers to implement."

1. Lead-Based
Paint As remodelers, you should already be familiar with the sticky issue of lead-based paint. The big thing to know is that there will be no changes to the current lead rules in Washington State for six months to two years. During this transition, you must continue to comply with OSHA laws governing lead-based paint on federal and tribal jobsites. Everyone from contractors, property managers, to those who serve paint are required to follow these steps, which apply to pre-1978 residential houses, apartments, and any places where children inhabit, like daycares or schools. Under the United States Environmental Protection Agency’s Lead-Based Paint Renovation, Repair, and Painting (RRP), construction firms must apply for and receive EPA Certification to disturb paint as part of their work in pre-1978 housing and child-occupied facilities. Anyone disturbing more than 6 sq. ft. (interior) & 20 sq. ft. (exterior) of lead-based paint must get the training.
Training requirements dictate that your supervisory person has to be certified if you're on a lead job. The rest of your employees also have to be trained, and know all the requirements that are specific to your job, including how to use a respirator. The ultimate goal is to eliminate BLLs (blood lead levels) in all adults that are higher than 10 μg/dl (micrograms/deciliter). Currently, you can still be on job site at 50 μg/dl.
I was asked “If the general contractor is lead certified doing work in a pre-1978 home, do subcontractors need to be lead certified as well?” The answer is no: If the general contractor did all the demo and cleaned up the site of all lead dust and debris prior to the sub beginning their work, the sub does not have to practice lead-safe work practices, and does not have to be a RRP certified renovator or firm. This information was confirmed by Dano Summers of the U.S. Department of Commerce. If something like this comes up, you can always call the Master Builders Association and we'll get involved however we can.
Firms who knowingly or willingly violate the RRP Program requirements could face penalties of up to $10,000 per day, per violation and/or face imprisonment. The fines hurt, and they’re getting bigger.
2. Crystalline
Silica Crystalline silica is tricky. It can become airborne during demolition and drilling—anywhere you would create dust. The final silica rule has a number of significant changes from the proposed rule, which will apply to a wide range of employers who are involved with common residential construction tasks such as using masonry saws, drills, jackhammers, performing milling, and heavy equipment for grading and excavating. Washington State has not yet authored a rule about crystalline silica, so unless you work on tribal property or federal lands governed by different jurisdictions, you have until June 23, 2017 to implement this rule.
The standard applies to all occupational exposures to respirable crystalline silica in construction work, except where employee exposures will remain below 25 micrograms. Examples of tasks with low exposures include mixing mortar; pouring concrete footers, slab foundation and foundation walls; removing concrete formwork; and finishing drywall.
There are two different ways to use the code: The first is a prescriptive path which details what you should do; the second is more of a performance-based path. These are some of the updates to the prescriptive paths:
- Companies with 50 or more employees are going to have to get their employees tested to measure where their exposure levels during and after the job. OSHA will come to the jobsite, take blood tests, and measure the limits. (Keep in mind that they only do that in high exposures.) Know ahead of time what exposure your employees could be experiencing.
- Workers must be protected from respirable crystalline silica exposures above the permissible exposure limit of 50 μg/m3 (micrograms of silica per cubic meter of air), averaged over an eight hour time weighted average (TWA) under any foreseeable conditions
- Employers can either use: 1) a control method in Table 1 of the construction standard; or 2) they can measure workers’ exposure to silica and independently decide which dust controls–if any are required—work best to limit exposures on the jobsite. Employers who follow Table 1 must fully and properly implement the engineering controls, work practices, and respiratory protection specified in the table. However, if done correctly— employers are not required to measure workers’ exposure to silica (i.e., perform exposure assessments/air monitoring) and are not subject to the PEL. These are the eighteen tasks that they actually have prescriptive paths for, if you have to be working in federal or tribal jurisdictions.
The 18 tasks identified in Table 1 include using the following equipment:

(Source: OSHA)
Alternative Exposure Control Methods
For tasks not listed in Table 1, or where employers do not fully and properly implement the engineering controls, work practices, and respiratory protection described in the table, employees alternatively must:
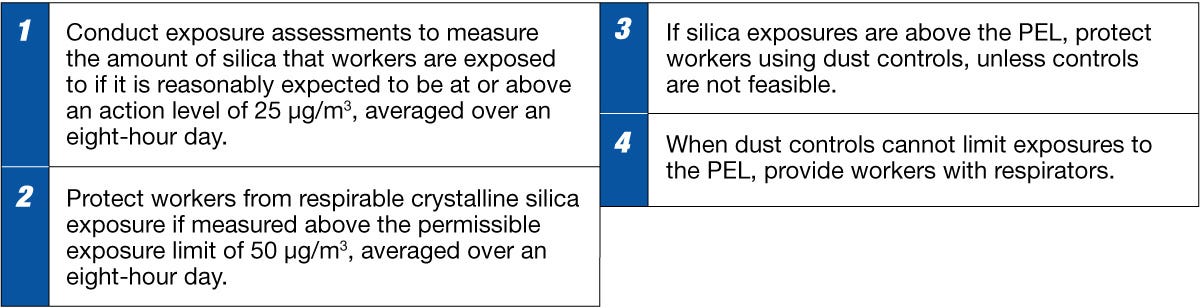
(Source: OSHA)
If you don’t use the prescriptive patch in Table 1, you will need to test for exposure risks and comply with the rule at the level of your workers' risk exposure. If they are over a certain level, you may need to furnish PPE respirators.
- For tasks performed using wet methods, water must be applied in sufficient quantity to minimize visible dust.
- Indoor tasks must minimize the accumulation of visible airborne dust.
- Enclosed equipment cabs must be maintained free from settled dust.
Of course, this is not a complete list of the prescriptive paths, but I’ve highlighted some of the most important ones. Following these regulations while working on federal and tribal lands will keep you and your employees protected and your business in compliance.
Al Audette is codes and regulations manager at the Building Industry Association of Washington, an organization dedicated to promoting the vitality of the building industry and the housing needs of the state’s citizens.