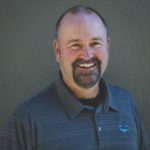
“I’ve gathered a number of plywood questions that we get asked again and again. Today, T.R. is answering them for me!”
From exterior wall sheathing to cabinetry, plywood serves countless uses and is one of the most ubiquitous building materials, especially here in the Pacific Northwest. With so many uses and different types of plywood available, it’s important to know your options, understand the material, and pick the right product for your project.
For our Plywood Series, we’re joined by T.R. Cauthorn, Panel Sales Manager at Hampton Lumber, a leading sustainable lumber producer based in Washington and Oregon and one of Dunn Lumber’s long-standing suppliers. With nearly 30 years spent with Hampton Lumber, plus experience working in mills and forests with Georgia Pacific, T.R. is a plywood expert.
In today’s episode, T.R.’s answering a selection of plywood-related questions we’ve gathered over the years, from how to best calculate the weight of a plywood order for shipping, to whether mills tend to vary in quality or not.
Watch our discussion in the video above or keep reading to get the highlights.
How do you calculate the weight of plywood when shipping?
It’s important to know how to determine the weight of plywood for the purpose of shipping—you don’t want to miscalculate and end up with a heavy load that will overload a truck or container or incur a potential fine.
Every 4x8 plywood panel is 32 square feet. Plywood suppliers typically measure and price plywood per 1,000 square feet (MSF), so to calculate the weight of a single panel, we take 0.032 multiplied by the specific product’s weight in pounds per MSF.
To do this, you need to know the approximate weight of different panel densities and thicknesses—more plys mean more weight.
0.032 x panel thickness weight per MSF = total weight
Some standard approximations are:
- 3/8” panel = 950 MSF
- 1/2” panel = 1,280 MSF
- 5/8” panel = 1,600 MSF
- 3/4” panel = 1,850 MSF
- 1 1/8” panel = 2,450 MSF
Let’s calculate the weight of a sheet of ½” CD four-ply as an example:
0.032 x 1,280 = 40.96 pounds per sheet
Once you know the pounds per sheet, you multiply that by the number of sheets in your order to come up with your total shipping weight.
What type of adhesive is used to make plywood?
The majority of plywood is made with exterior glue. Hardwood plywood, mostly used for building things like furniture and cabinets, is made with different types of glue to achieve a different finish and color.
What are the most common plywood panel sizes?
Today, the most common plywood panel sizes are:
- Four-by-eight (4’ x 8’)
- Four-by-nine (4’ x 9’)
- Four-by-ten (4’ x 10’)
Some mills also produce:
- Five-by-eight (5’ x 8’)
- Five-by-nine (5’ x 9’)
- Five-by-ten (5’ x 10’)
If you need a different size, such as a larger sheet, you’ll need to go to a custom shop.
Why are there different numbers of plys used for ½" sheathing panels?
For sheathing panels, you’ll find ½” panels in three-ply, four-ply, five-ply, and five-ply structural. Three-ply isn’t as widely produced these days because it requires 1/6" veneer. That's because 1/6" veneer is needed to make ¾" CD panels, which is what mills prefer to use it for. Something like a ½" four-ply is more common, and that panel is made with 1/8" veneers. Five-ply structural sheathing is made with 1/10" veneer and is manufactured to meet more stringent engineering requirements.
What’s the range of plywood panel thicknesses available?
The thicker the panel, the longer it needs to be pressed together. Because of that, most mills won't press panels thicker than 1 1/8". When it comes to producing industrial panels (which come with a higher price tag), mills usually go up to 1 ½" in thickness.
What is the thickness tolerance for plywood?
The APA has specific product standards to ensure panels being sold at the same thickness are as consistent as possible. That said, there can be slight variations from panel to panel, or panels from one mill compared to panels from another. Mills mix and match different veneer thickness (depending on what is available), to arrive at the desired thickness of the final product; always meeting the minimum thickness dictated by the product standards.
On the same note, there are also different ways to make a product like ¾" CD; the same panel thickness can be made with four-ply or five-ply depending on the veneer thickness. However, as long as it meets product standards, this mix-and-match process doesn't affect the grade stamp on the final product.
Do some mills produce better plywood than others?
There can be some quality differences between mills, and some mills may produce certain materials that other mills don’t. That said, the mills still operating in the U.S. and Canada today are all well run and meet high standards while collectively offering a wide range of materials. The choice is up to you on what level of quality you need in your plywood for a particular project.
At Dunn Lumber, our premium core plywood underlayment panel is custom made with a B face that doesn’t have any knots or voids and a solid core interface. This custom product is designed to withstand sharp objects, such as high heels or table legs. We always strive to have the highest quality panels the industry has to offer.
Learn more, see what’s in stock, and get personalized help at any of our Dunn Lumber locations located throughout King County and Snohomish County.
You can also learn more about plywood by watching other episodes in this series covering topics like how plywood is made, the difference between plywood and OSB manufacturing, and the history of plywood in the Pacific Northwest.